标准催化剂在大连石化渣油加氢装置首次应用
甘彬彬(中国石油大连石化分公司,辽宁大连 116032)
【摘要】本文介绍大连石化渣油加氢装置的工艺技术特点,以及标准公司渣油加氢催化剂在大连渣油加氢装置第三周期的应用,包括催化剂装填、装置开工过程以及装置运行情况。结果表明,标准公司的催化剂具有较高的加氢脱硫、脱残炭、脱金属活性和活性稳定性,以 20w%常压渣油和 80w%减压渣油混合原料,可以生产出硫含量小于 0.35w%,残炭含量小于
5.5w%,金属含量小于 15mg/kg的加氢常渣产品,且预计装置运行周期可达到 21个月。【关键词】渣油加氢催化剂工艺周期
1、概述
大连石化 300×104t/a渣油加氢脱硫装置采用美国雪佛龙公司( CLG)固定床渣油加氢脱硫工艺技术,以俄罗斯常渣、俄罗斯减渣、沙轻减渣为原料,经催化加氢反应,脱除硫、氮、金属等杂质,降低残炭含量,为催化裂化装置提供加氢常渣产品硫含量不大于 0.35%(质量分数)、残炭不大于 5.5%(质量分数)、Ni+V不大于 15μg/g的原料,同时生产部分柴油,并副产少量石脑油和燃料气。
本装置为目前国内处理能力最大的渣油加氢装置,其工艺特点如下 : 1)反应部分设置两个系列,
每个系列可以单开单停(单开单停是指装置内两个系列分别进行正常生产和停工更换催化剂)。由于
渣油加氢脱硫装置的设计操作周期与其他主要生产装置不一致,从全厂生产安排的角度,单开单停
可以有效解决原料储存、催化裂化装置进料量等问题,并使全厂油品调配更加灵活。2)反应部分
采用热高分工艺流程,减少反应流出物冷却负荷;优化换热流程,充分回收热量,降低能耗。3)
反应器为单床层设置,易于催化剂装卸,尤其便于卸剂。4)采用炉前混氢流程,避免进料加热炉
炉管结焦。5)循环氢脱硫塔前设高压离心式分离器,以除去携带的液体烃类,减少循环氢脱硫塔
的起泡倾向,有利于循环氢脱硫的正常操作。 6)设置高压膜分离氢提浓设施,保证反应氢分压。 7)
冷低压闪蒸罐的富氢气体去加氢裂化装置脱硫后,去 PSA装置回收氢气。8)分馏部分采用主汽提
塔-分馏塔流程,在汽提塔除去轻烃和硫化氢,降低分馏塔材质要求。 9)催化剂预硫化按液相预硫
化方式设置。2、催化剂系统
通过技术交流和综合比较,渣油加氢装置第三周期 1系列催化剂选择标准公司的渣油加氢催化剂。根据中试实验结果和其它工业应用经验,标准公司推荐多种保护剂级配方案,以确保在整个运转周期内,保持较低的反应器压降。针对大连石化存在残炭难脱除的问题,加强催化剂的脱残炭能力,标准公司对主催化剂组合(见表 1)进行优化,增加了脱硫、脱残炭催化剂比例,减少了脱金属催化剂比例,以达到最好的脱硫、脱残炭、脱金属效果。
表 2.1 催化剂体系
催化剂 | 尺寸, mm | 形状 | 装填堆比, kg/m3 |
---|---|---|---|
RM-5030 | 5.6 | 三叶草 | 420 |
RM-5030 | 2.5 | 三叶草 | 430 |
RM-5030 | 1.3 | 三叶草 | 430 |
RN-412 | 1.3 | 三叶草 | 577 |
RN-5210 | 1.3 | 三叶草 | 595 |
RN-650 | 1.3 | 三叶草 | 568 |
RN-888 | 1.3 | 三叶草 | 703 |
3、催化剂装填与装置开工
时间 | 工作内容 | 备注 |
---|---|---|
6月 4日 11:00 | 催化开始装填 | |
6月 10日 2:00 | 1系列催化剂装填结束 | 用时 133小时 |
6月 20日 18:00 | 界面交接,投用公用工程 | |
6月 21日 8:30 | 两系列反应系统引中压氮气系统升压气密 | |
17:10 | 低压系统氮气气密置换 | |
6月 22日 17:10 | 低压火炬并网 | |
6月 23日 8:00 | 所有塔罐置换合格拆界区盲板 | |
15:00 | 高压火炬并网 | |
16:00 | 引柴油、拆瓦斯盲板,原料分馏系统冷油运 | |
6月 24日 10:00 | 开 K1801-2 | |
14:00 | 开 K1801-1,点 F1801-1/2,系统升温,催化剂干燥 | |
6月 26日 8:00 | 所有温度点达到 93.3℃以上,催化剂床层温度均 >150℃ | |
9:00 | 系统开始升压气密,速度 1.0MPa/hr | |
6月 27日 12:00 | 急冷氢试验,未做紧急泄压试验 | |
16:00 | 开 P1802-2,反应部分进油冲洗、浸润 | |
17:10 | F1801-2点 16个主火嘴 | |
16:50 | 开分馏塔底泵 P1810 | |
17:55 | 开分馏炉对流段循环水泵 P1821S | |
18:30 | 开 P1802-1,反应部分进油冲洗、浸润 | |
19:50 | V1803-2见液位 | |
6月 28日 00:50 | V1803-1见液位 | 器壁 T<100℃ |
4:00 | 冲洗结束转热长循环,注 DMDS,2.5t/h,4t/h | |
停收罐区柴油,FV8104、FV8204付线开 | ||
注 DMDS后反应器入口向 235/232℃升温恒温硫化 | ||
15:30 | 硫化氢穿透,1列 7039mg/m3,2列 15319mg/m3 | |
16:00 | 两系列炉出口向 245℃提温 | |
19:30 | 引蜡油进两系列 | |
21:30 | 投注水 | |
6月 29日 4:00 | 常渣采样全为 VGO,部分转循环,外送改至西油槽 | |
6:00 | 停硫化剂 | |
14:30 | 两系列反应器入口升至 310℃,引罐区常渣,降 VGO | 10t/h.列 |
20:35 | 开贫胺泵,建立胺循环 60t/h.列 | |
21:00 | 开中段回流泵建立中段回流 | |
6月 30日 9:00 | 停循环油,装置进料全部为常渣 | |
16:00 | 反应进料量提至 185t/h。循环氢压缩机转速提至 9200r/min;CAT提至 330℃ | |
7月 1日 14:00 | 装置所有产品合格,转合格线。 | |
7月 8日 13:00 | 1系列 CAT升至 369℃,以 10t/h引三蒸馏减渣 | 开工正常 |
4、装置运转情况
4.1 装置 1系列第三周期运转总体状况
渣油加氢装置1系列第三周期催化剂至 2012年6月30日共运行365天,累计加工量 1561426t,其中渣油1543534t,氢气 17892t,平均日加工渣油 4228t。第三周期加工的原料有三蒸馏减渣、一蒸馏常渣,平均加工负荷为94.50%,其中1系列第三周期物料平衡见表2。
表4.1 第二周期物料平衡表
项目 | 加工量/t | 比例,% | ||
---|---|---|---|---|
入方 | 原料油 | 1543534 | 100.00 | |
工业氢 | 17892 | 1.16 | ||
合计 | 1561426 | 101.16 | ||
出方 | 加氢常渣 | 1338997 | 86.76 | |
柴油 | 129368 | 8.38 | ||
粗石脑油 | 37526 | 2.43 | ||
其他 | 55535 | 3.59 | ||
合计 | 1561426 | 101.16 |
- 2设计原料、产品性质及操作条件
- 2.1原料性质表 4.2 第三周期原料性质
- 新氢气性质装置补充氢气来自氢气管网和膜分离提浓氢。
项目 | 设计原料性质 | 第三周期报价原料性质 |
---|---|---|
数量(两系列),t/d | 8955 | 8955 |
密度(20℃),kg/m3 | 998 | 998 |
粘度(100℃),cst | 320 | 320 |
MCR, w% | 17.0 | 17.0 |
S, w% | 3.9 | 3.2 |
N, w% | 0.52 | 0.36 |
沥青质(C7不溶物),w% | 5.4 | 5.8 |
金属含量 Ni+V, PPmwt | 87 | 60 |
蒸馏数据 ASTM D1160 v% | ℃ | |
2 | 355 | |
10 | 509 | |
22 | 531 |
表 4.3 新氢性质
组成 | H2 | CH4 | ∑ |
---|---|---|---|
mol% | ~98 | ~0.1 | 100.0 |
温度:40℃压力:2.4MPa(G)
- 2.3加氢渣油性质表 4.4 渣油产品性质
- 2.4主要操作条件
- 表 4.5 主要操作条件
- 催化剂实际运行及硫、残炭、金属脱除情况为考察催化剂运转状况,对从 2011年 6月开工以来的运转数据进行整理。
- 反应温度和反应器压降
项目 | 设计指标 | 报价指标 |
---|---|---|
馏程 | >350℃ | >350℃ |
S, w% | ≯0.35 | ≯0.35 |
Ni+V , PPmwt | ≯15 | ≯15 |
CCR, w% | ≯5.5 | ≯5.5 |
运转周期 | 8000小时 |
---|---|
体积空速,h-1 | 0.2 |
原料油流量, t/d | 4477.5 |
反应氢分压 ,SOR/EOR,MPa | 17.4/17.1 |
气油比,SOR/EOR | 759 |
反应器入口压力, SOR/EOR,MPa | 19.45/19.88 |
一反入口温度,℃ | ≤370 |
在图 4.1中列出了装置的平均温度( CAT),可见图中分别在第 45天,120天以及 320天有三处突变,第一处为装置停工处理柴油塔底再沸器,第二处为新区除渣油和重整外,其余装置停工消缺,装置降温降量,第三处为四催化停工检修,全厂加工低硫原油,导致装置进料硫含量等杂质含量均降
低,催化剂放热量减少,使反应进料温度降低,催化剂平均温度(CAT)也降低。
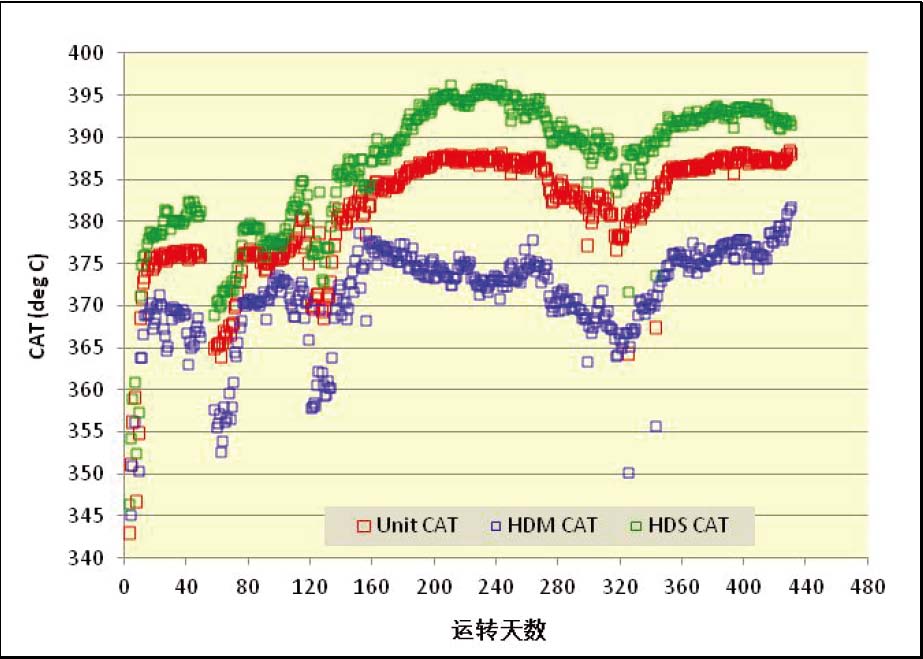
图 4.1 第三周期 1系列平均温度
在图 4.2中列出了每个反应器的压降,从中可以看出一反的压降从初期的 0.10MPa,运转到第 430天,一反的压降达到 0.15MPa,此外其它各反应器床层压降控制也比较好。从中可以看出装置自动反冲洗过滤器投用运行良好,标准公司推荐级配装填非常合理,以及催化剂结焦情况稳定,未造成压降大幅上升,保证了催化剂的长周期运行。
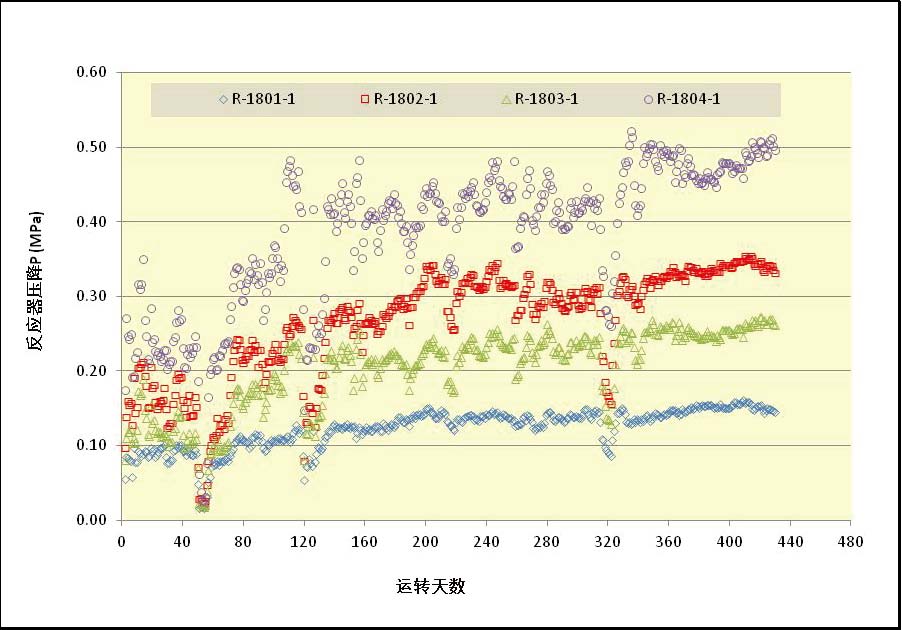
图 4.2 第三周期 1系列压降情况
4.3.2 脱硫情况

图 4.3 第三周期 1系列原料硫和渣油产品硫含量对比
原料硫含量和渣油产品硫含量见图 3,可以看出原料硫含量在 1.2%~3.6%(质量分数)之间,产品硫含量在 0.1%~0.45%(质量分数)之间,在 70天至 270天内,原料硫含量稳定在 2.4%~3.2%(质量分数)产品硫含量均在 0.22~0.4%(质量分数),能够满足现有生产要求。为了将催化剂的运行周期从设计的 11个月延长到 21个月,在实际生产过程中,对催化剂升温速度进行了一定的控制,同时相应放宽了产品硫含量指标。
4.3.3 脱残炭情况
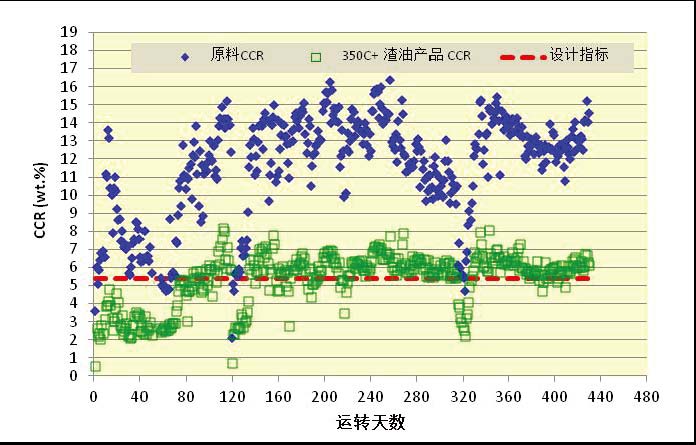
图 4.4 第三周期 1系列原料残炭和常渣残炭含量对比图
从图 4中原料残炭含量和产品常渣残炭含量可以看出,原料残炭含量在 5w%~17 w %(质量分数)之间,产品残炭含量在 2 w %~7 w %(质量分数)之间。其中在 70天至 270天内原料残炭含量在 11%~16%(质量分数)之间,产品残炭含量在 4.5 w %~7 w %之间,且大部分数据在 6 w %左右,略高于设计指标 5.5%,主要原因是为了延长催化剂的运行周期,对催化剂提温速度进行了控制,相应放宽了产品残炭指标。
4.3.4 脱金属情况
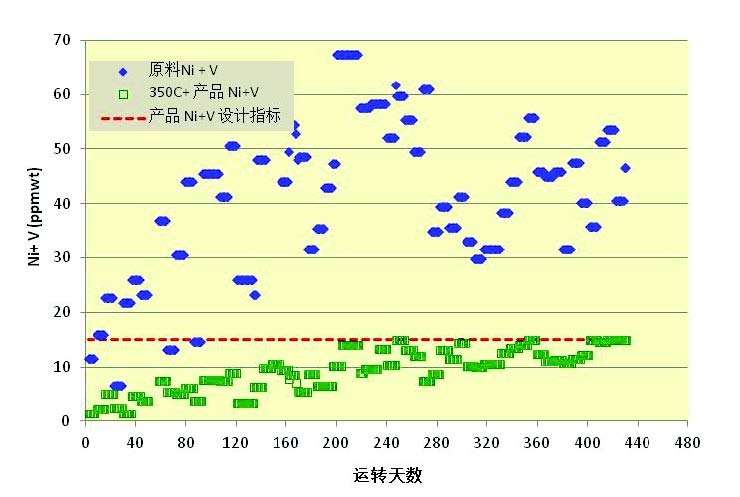
图 4.5 第三周期 1系列原料残炭和常渣残炭含量对比图
原料金属含量和产品常渣金属含量对比图 4可以看出,原料金属含量在 30~68mg/kg之间,产品金属含量在 15mg/kg以下,完全满足生产要求。
4.3.5 装置催化剂标定情况
由于装置有两系列反应部分,为对催化剂的性能进行考核,装置与 2011年 12月 7日、8日、13日、14日分别对对原料和热低分油样进行采样分析,原料油采样时间为每天 6时,热低分油采样时间为每天 9时,以下为杂质脱除率:
表 4.6 杂质脱除率统计表( w%)
杂质脱除率 | 设计值 | 12月 7日 | 12月 8日 | 12月 13日 | 12月 14日 | 平均值 |
---|---|---|---|---|---|---|
脱硫率 | 91.0 | 88.7 | 88.6 | 89.9 | 92.2 | 90.1 |
脱氮率 | 55.8 | 42.9 | 41.7 | 47.4 | 52.5 | 48.1 |
脱残炭率 | 67.7 | 51.4 | 56.6 | 59.8 | 67.0 | 60.5 |
脱金属率 | 82.8 | 81.1 | 84.3 | 87.5 | 87.1 | 84.6 |
由以上数据可知,热低分油脱硫率和脱金属率接近设计值,脱残炭率和脱氮率低于设计值,主要原因为原料中残炭含量和氮含量远远低于设计值,在目前的反应温度下加工此种原料,催化剂体系的脱金属能力没有任何问题,脱硫能力很强基本能达到要求,脱残炭和脱氮能力还需进一步提高反应温度。
5、结论
- )标准公司渣油加氢催化剂具有稳定的加氢脱硫、加氢脱残炭、加氢脱金属活性,以常渣和减渣混合原料作为设计原料,可以生产出硫含量小于 0.35%(质量分数),残炭含量小于 5.5%(质量分数),金属含量小于 15mg/kg的加氢常渣,满足催化裂化装置要求。
- )渣油加氢装置自开工以来,原料温度一直未达到设计值(150℃),导致反应加热炉负荷长期处于满负荷运行,加之全厂瓦斯组分不稳定,最终导致一反入口温度不稳定,且不能达到催化剂所要求的一反入口温度。此外,由于全厂物料平衡的需要,以及渣油加氢、减渣的进料比例由设计时的 80%调整为 80%~90%,导致装置脱残炭和脱硫难度加大。
3)根据目前运行情况,预计装置可以运转到 2012年 4月份,达到 21个月的运行周期。